Sample preparation
GATAN 691 PIPS I Ion Milling Machine
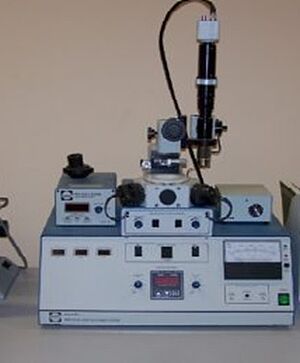
PIPSI is an Ar ion-milling machine working with two Penning ion guns aimed to the sample at angles between 0 and 10 °. The low angles have the advantage of minimizing the damage caused by irradiation and beam heating while at the same time producing samples with electron-transparent areas with minimal artefacts. It is possible to work at low temperatures. The ion energy can be varied from 1 keV to 6 keV by choosing between double or single sector beam modulations. The beam diameter is about 800 µm FWHM at 5 KeV. The mounting of the 3 mm specimen is done on GATAN single side specimen holders. The rotation of the sample can be varied from 1 to 6 rpm and specimen-viewing window is protected by a pneumatically operated shutter shield. The vacuum systems consists of oil-free pumps - a diaphragm pump and molecular pump reaching pressure of 5x10-6 Torr base pressure and 2x10-5 to 2x10-4 Torr operating pressure.
Applications: TEM thin foils for vast range of materials (ceramics, metals, minerals).
GATAN 695 PIPS II Ion Milling Machine
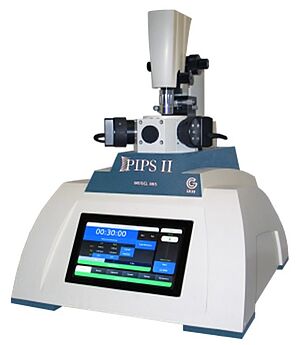
It is a second-generation precision ion polishing instrument for the preparation of thin samples for TEM. Both ion guns are motorized and they can operate from 100 meV to 8 kV with an inclination angle of ± 10 °. The low limit of 100 eV allows a very smooth polishing at the end of preparation. A new low energy-focusing electrode provides a constant beam diameter across the sample over the entire energy range. The beam size at 100 meV is 500 μm FWHM. The PIPS is equipped with a sample X and Y displacement platen for accurate positioning of the target area. A turbo molecular secondary pump and a membrane primary pump keep the environment ultra clean. The thinning can be performed with beam modulation in single and double sectors. Angular ranges of sectors of thinning are variable and programmable. The system is also equipped with a cold module to thin temperature sensitive materials. It is equipped with a Zoom digital microscope with a Digital Micrograph computer control system for in situ observation of samples.
Applications: Clean FIB samples; final milling of a classical cross-section or plane-view samples.
Fishione SEM Mill 1061
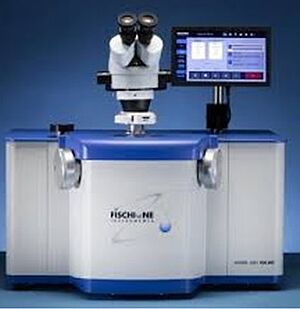
The Fishione SEM Mill 1061 ion polisher is a polishing system for preparing samples for scanning electron microscopy. It is equipped with two argon ion guns independently adjustable in voltage (100V to 10kV) and angle (0 to 10 °). The system incorporates an airlock ensuring fast sample transfer without degrading the chamber vacuum. The polisher accepts samples up to 32 mm in diameter and 25 mm in thickness. The surface of the sample is automatically identified by the system, ensuring optimal positioning of the surface to be milled. A touch screen is used to adjust the main polishing parameters (polishing time, sample rotation, voltages and gun angles). Etching can be controlled during ion milling process with an optical microscope. The system also offers the possibility of cross-sections thanks to special sample holders. Finally, it is possible to work at low temperatures thanks to a liquid nitrogen cooling system built into the polisher.
Applications: Smooth surface quality for some SEM analysis (EBSD in particular) on a wide variety of materials (metals, minerals and others). Achievement of planar polishing and cross-section.
GATAN 682 Precision Etching and Coating System (PECS)
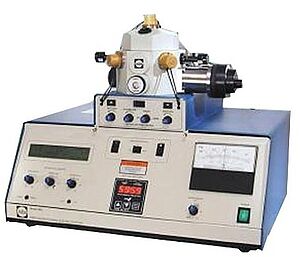
PECS deposits extremely thin coatings (a few nanometers) of a metal (chromium, carbon, platinum, gold ...) on samples for observation by SEM and TEM. The target material is bombarded under secondary vacuum by two argon ion beams accelerated between 2 and 8 kV. The ejected target material then strikes the surface of the sample which can be rotated and tilted at different angles during the deposition process. The deposited metal thickness is controlled by a quartz scale.
Application: Deposite of chrome, carbon, platinum.
Ultra Microtome and Cryo-ultra Microtome UC7
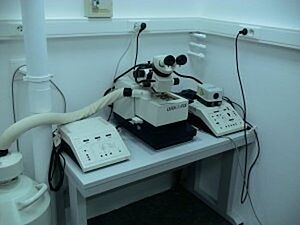
Ultra microtomy is a method of cutting samples in extremely thin slices of the order of 70 nm for a TEM analysis, using diamond knives. This technique can also be used for SEM and AFM preparation by surfacing samples. Initially this technique was used by biologists, but it is currently used to cut many materials (composites of the type polymers-soft metals...). There is the possibility of working at a very low temperature by cooling with liquid nitrogen for materials that can not be cut at ambient temperature.
Applications: Polymer sections for TEM, powder dispersed in a resin.
MultiPrep™ Semi-automatic Polishing System
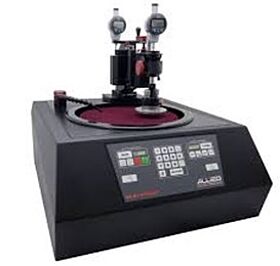
The MultiPrep system allows semi-automatic precision polishing of samples for microscopy (optical, SEM, TEM etc.). It is mainly used for the preparation of samples in cross-section. Two micrometers and the semi-automatic polishing shoulder allow precise adjustments of the tilt of the sample relative to the abrasive plane and allow to control with a micrometric precision the amount of material removed during polishing. The polishing is carried out thanks to a plastic film containing diamond grains with a thickness of 30 to 0.1 μm. Final polishing can be done with colloidal silica (0.02 to 0.05 μm powder) on a textile sheet.
Applications: TEM foils and SEM samples.
Buehler IsoMet™ Low Speed Cutting Machine
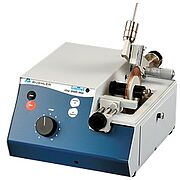
The most commonly used method for abrasive cutting of materials. Cut-off wheels consist of two main components: abrasives and binders. During cutting, the cut-off wheel is rinsed with a coolant to prevent thermal damage and to remove debris, thereby removing as much material as possible. This cutting machine covers the entire spectrum of materiality from a delicate precision cut to cutting large objects. Slow cutting speed is possible.
Applications: TEM and SEM samples.
Dimpler
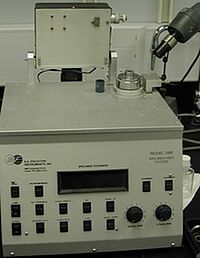
The Dimpler is a precision instrument used for grinding circular dimples in the surface of materials. The sample is placed on a horizontal plane rotating around a vertical axis and a grinding wheel rotating around a horizontal axis. The dimple technique produces with minimal damage a thin region in the disk (thickness less than 50 μm) while leaving a relatively thick support border surrounding the thin region and thus providing a very robust sample. A chemical or ion thinning then makes it possible to obtain large transparent areas.
Applications: Many materials can be dimpled (ceramics, metals, minerals, glasses, etc).